Kiểm Tra Áp Lực Cho Van Trong Thiết Kế Đường Ống (Valve Pressure Test)
- Happy
- Jan 2, 2021
- 6 min read
Updated: May 11, 2021
Chào các độc giả thân thương của pipingdesigners. Một năm 2020 sắp trôi qua, năm 2021 đang đến gần, chúc các độc giả của pipingdesinger có một năm 2021 nhiều hạnh phúc và thật thành công nhé.
Van là một trong những thành phần vô cùng quan trọng năm trên đường ống. Chúng được sửa dụng trong tất cả các công trình dầu khí để (1) đóng – mở dòng chảy, (2) điều tiết lưu lượng, (3) chống chảy ngược và (4) điều chỉnh, tăng giảm áp. Pipingdesigners đã có 4 bài viết để làm quen với van rồi, các bạn còn nhớ không nào? Truy cập link phía dưới nếu bạn nào chưa đọc nhé!
Với vai trò quan trọng trong đường ống, van phải đảm bảo các yêu cầu nghiêm ngặt từ khâu thiết kế tới vận hành. Để việc vận hành van được đảm bảo trơn tru, hoạt động đúng chức năng, công tác kiểm tra áp lực được yêu cầu thực hiện tại ngay nhà máy sản xuất và trước khi mang ra công trường lắp đặt, ít nhất là thực hiện hai lần kiểm tra áp lực trong các công trình dầu khí.

Tại sao phải thực hiện ít nhất 02 lần? Nếu đã qua kiểm tra áp lực van ở nhà máy, thì tại sao cần phải thực hiện kiểm tra lại tại nơi sử dụng trước khi lắp đặt làm gì? Có độc giả nào thắc mắc như vậy không?
Van sau khi được chế tạo tại nhà máy, bắt buộc phải thực hiện kiểm tra áp suất ngay tại nhà máy. Việc này đảm bảo van không bị rò rỉ khi được hoạt động dưới áp suất thiết kế. Nếu phát hiện rò rỉ, nhà máy sẽ thực hiện khắc phục sửa chữa ngay lập tức.
Các công trình dầu khí ngoài khơi có vòng đời hầu hết trên 20 năm, được vận hành trong môi trường biển, có hàm lượng ăn mòn cao. Chính vì thế, van thường được sơn (coating) một lớp bên ngoài để kéo dài tuổi thọ của van. Sau khi hoàn thành kiểm tra áp lực đạt các điều kiện cho phép, van được mang đi sơn, sau đó đóng gói vận chuyển tới đơn vị mua hàng (end user).
Sau khi van về tới kho, để đảm bảo van không bị rò rỉ, van sẽ được thực hiện thử áp lực lại một lần nữa trước khi mang ra công trường lắp đặt. Trong quá trình sơn, mỗi nhà sản xuất / nhà thầu sơn sẽ có một quy trình sơn khác nhau, trong đó công tác che chắn van để bắn hạt mài (sandblast) trước khi sơn có ảnh hưởng lớn tới việc rỏ rỉ van.

Các hạt cứng trong quá trình sandblast nếu không được che chắn cẩn thận, sẽ đi vào bên trong body của van, dưới tác động của lưu chất có áp suất sẽ làm cho chúng chèn vào các khe hở, làm cho van không kín khi đóng, gây hiện tượng rò rỉ.
Việc thực hiện thử áp lực một lần nữa tại xưởng của đơn vị sử dụng (end user) nhằm phát hiện và khắc phục tình trạng rò rỉ do hạt cứng nếu có.
Có độc giả nào thắc mắc rằng tại sao không thực hiện sơn xong rồi hãy thử áp lực tại nhà máy? Như thế có tiết kiệm thời gian và chi phí hơn không? Ý tưởng này thoạt đầu nghe rất hợp lý nhưng vẫn tiềm ẩn nhiều rủi ro khó lường. Van được thực hiện thử áp suất tại nhà với điều kiện không sơn để phát hiện các rò rỉ gây ra do sự không kín khít giữa các chi tiết, và đặc biệt là các vết nứt ngầm (micro crack) bên trong mà mắt thường hoặc các phương pháp NDE không thể phát hiện ra được. Nếu sơn, các layer sơn sẽ vô tình như một lá chắn, che phủ các vết nứt siêu nhỏ đó, không thể phát hiện rò rỉ. Trong vòng đời vận hành, các vết nứt đó sẽ lớn dần và trở nên vô cùng nguy hiểm.
Mặc dù việc thử áp lực tại nơi sử dụng trước khi lắp ngoài công trình tiêu tốn tiền bạc và thời gian, nhưng đó là một trong những phương án tối ưu nhất để đảm bảo van được vận hành trơn tru trên giàn. Giảm thiểu rủi ro rò rỉ ngoài công trường khi phải tháo ra sửa chữa / thử áp lại.
Các tiêu chuẩn quốc tế thường được áp dụng trong công tác thử áp như sau:
- ASME B16.34 Valves-Flanged, Threaded and Welding Ends
- API 598 Valve Inspection & Testing
- API 6D Specification for Pipeline Valves
- API 600 Bolted Bonnet Steel Gate Valves
- ISO 5208 Industrial Valves – Press. Testing of Metallic Valves
- DIN EN 12266 Industrial Valves – Testing of Valves
- MSS-SP-61 Pressure Testing of Steel Valves
Bảng áp dụng các tiêu chuẩn tương ứng cho thử áp lực từng loại van được thể hiện ở bảng dưới.

Lưu chất dùng trong thử áp lực:
Lưu chất thường được sử dụng trong thử áp suất cao là nước sạch chứa làm lượng chất ức chế ăn mòn nhất định ở nhiệt độ môi trường (thường 5oC tới 38oC). Hàm lượng chloride trong nước không được vượt quá 30µg/g.
Lưu chất thường được sử dụng trong thử áp suất thấp là khí trơ như N2. Tùy thuộc vào đặc thù mỗi dự án, khí N2 có thể được yêu cầu sử dụng trong thử áp suất cao cho seat của van. Nếu yêu cầu thử khí áp suất cao cho body thì khí thường được sử dụng là 99% N2 + 1% He.
Phân loại thử áp lực van thường gặp:
1. Kiểm tra body van – hydrostatic shell test
- Van được ép chặt 2 đầu trên thiết bị kiểm tra thủy lực chuyên dụng (test bench) hoặc sử dụng bích mù để làm kín van.
- Vặn van để mở 50% để toàn bộ các chi tiết chịu áp (pressure containing part) sẽ bị tác động bởi áp suất thử và để tránh rủi ro làm hỏng seat bên trong van.
- Điền đầy các khoang trống của van (valve cavity), nếu có, bằng lưu chất thử trước khi thực hiện gia áp.
- Thực hiện bơm ép lưu chất bằng cách gia áp tới giá trị gấp 1,5 lần áp suất thiết kế.
- Theo dõi đồng hồ đo áp để kiểm tra áp suất có được duy trì hoặc bị rò rỉ hay không.
- Ghi chép kết quả và so sánh với các tiêu chuẩn chấp nhận tương ứng (rò rỉ không được cho phép đối với thử body van)
2. Kiểm tra seat van áp suất cao - the high pressure closure test or valve seat leak test
- Van được ép chặt 2 đầu trên thiết bị kiểm tra chuyên dụng (test bench) hoặc sử dụng bích mù để làm kín van.
- Vặn van để mở 50%
- Điền đầy các khoang trống của van (valve cavity), nếu có, bằng lưu chất thử trước khi thực hiện kiểm tra.
- Vặn van để đóng 100%
- Thực hiện bơm ép lưu chất bằng cách gia áp tới giá trị gấp 1,1 lần áp suất thiết kế.
- Theo dõi đồng hồ đo áp để kiểm tra áp suất có được duy trì hoặc bị rò rỉ hay không.
- Ghi chép kết quả và so sánh với các tiêu chuẩn chấp nhận tương ứng.
3. Kiểm tra seat van áp suất thấp - the low pressure closure test or valve seat leak test
Thực hiện tương tự như kiểm tra seat van áp suất cao nhưng lưu chất sử dụng là khí, và áp suất kiểm tra thấp 4 – 6 bar tùy theo tiêu chuẩn dự án.
4. Kiểm tra backseat – Backseat Test, áp dụng với các loại van cấu tạo có backseat (Globe, Gate)
- Van được ép chặt 2 đầu trên thiết bị kiểm tra thủy lực chuyên dụng (test bench) hoặc sử dụng bích mù để làm kín van.
- Điền đầy các khoang trống của van (valve cavity), nếu có, bằng lưu chất thử trước khi thực hiện gia áp.
- Mở van 100% và nới lỏng bộ phận packing gland hoặc tháo rời hẳn ra
- Thực hiện bơm ép lưu chất bằng cách gia áp tới giá trị gấp 1,1 lần áp suất thiết kế.
- Ghi chép kết quả và so sánh với các tiêu chuẩn chấp nhận tương ứng (rò rỉ không được cho phép đối với kiểm tra backseat).
Các tiêu chuẩn áp dụng cho từng loại kiểm tra áp suất van được thể hiện như bảng dưới:

R – Bắt buộc O: không bắt buộc A: có thể thay thế, ở trường hợp này là kiểm tra shell bằng khí có thể thay cho kiểm tra bằng nước.
Bảng chi tiết cho từng loại kiểm tra áp suất được tổng hợp ở các bảng dưới:
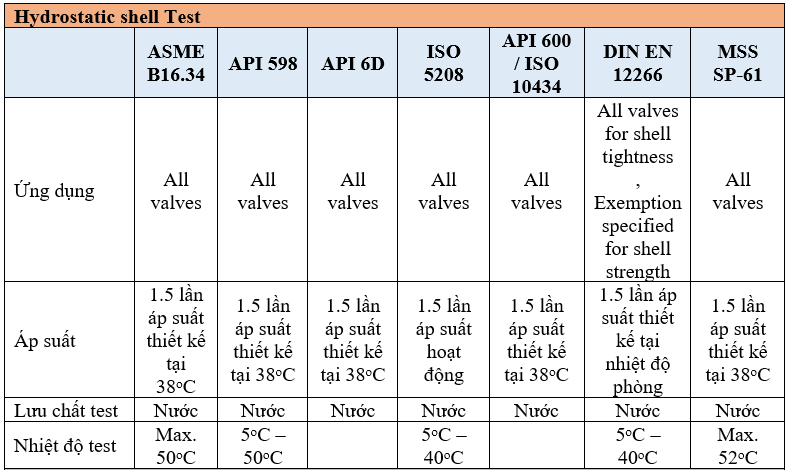


Như vậy các độc giả đã cùng Pipingdesigners tìm hiểu thêm một công tác kiểm tra trong thiết kế đường ống rồi phải không nào. Hãy cùng đón nhận những bài viết sâu hơn về van nhé. Thank you!
Comments